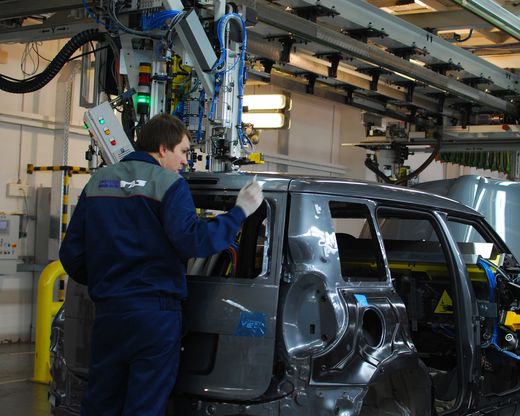
Редкий случай – по заводу нас водил инженер, отвечавший за
проект нижегородского предприятия Volkswagen/Skoda,
чех по национальности, один из отцов местного производства. Я придумал мнемоническое правило для его имени:
социальная сеть + эта смуглая американская актриса… В общем, его зовут Фейсбук
Лопес. Стоп, нет. Твиттер Энистон. Нет… Моймир Хайек. Да, точно так. Ну или почти.
Так вот, господина Хайека можно спросить: «А что это за
ерунда вот там мерцает?», и он внятно ответит: «Дело в том, что скорость
транслатеральной инфузии в анизотропных средах…» В общем, наш человек, технарь.
Он гордится, что от проекта до запуска завода в Нижнем
Новгороде прошло 11 месяцев, и что это – одно из самых современных предприятий Volkswagen, круче многих
европейских. Заводы ведь, как и машины, постоянно совершенствуются, и чем позднее построен завод, тем он более
инновационный. 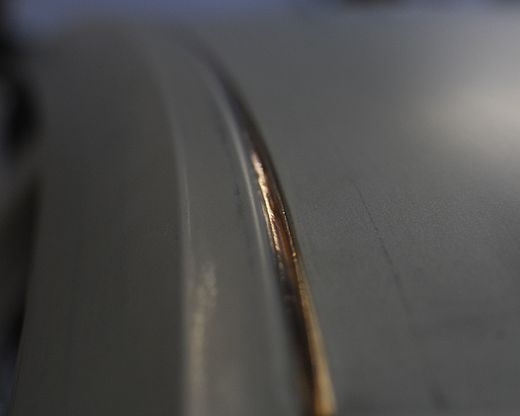
Вот, например, лазерная пайка – дорогостоящий с точки зрения
инвестиций, но почти идеальный процесс соединения стальных деталей. Шовчик
получается тонким, красивым, как бобслейный желоб, прямо ювелирным, и если у Yeti таким способом
припаивают только крышу, то у новой Octavia лазерных швов будет больше – 6,2 метра против 1,2. А
значит, что? Значит, будет меньше точечной сварки: 3338 (Октавия) против 4690
(Йети) точек. Это, кстати, одна из причин легкости новых шасси на платформе MQB, на которой строится
новая «Октавия»: возрастает жесткость соединений, снижается металлоемкость.
А вот три специальных сварочных стенда, где в полностью
автоматическом режиме крупные кузовные детали устанавливаются с очень высокой
точностью и прихватываются сваркой, чтобы впоследствии человеческий фактор не
влиял на геометрию кузова.
Или еще одно ноу-хау – воскование кузова. В отдельном цеху уже
окрашенные кузова попадают в специальную камеру, где из 16-тонной ванны с
расплавленных воском десятки форсунок закачивают его в скрытые полости машины –
по 3,5 кг на брата. Воск, по консистенции и цвету похожи на сгущенку, заполняет
потенциальные очаги коррозии. 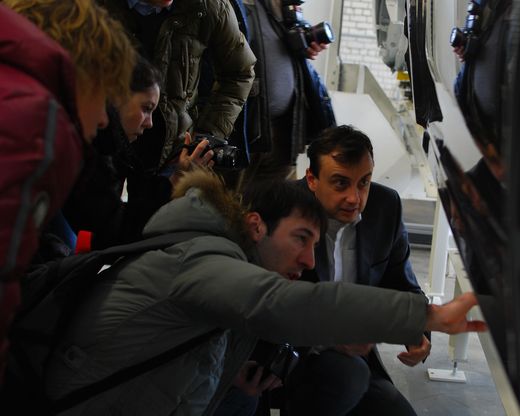
Моймир Хайек с азартом объясняет, куда заливается воск
Собственно, разговор с Фейсбуком… с Моймиром начался не с этого:
меня интересовало, какова субординация между концерном Volkswagen и группой «ГАЗ». Например,
кузовной цех, где сейчас кудесничают 137 роботов Kuka – это то
самое место, откуда когда-то выкатывались «Волга» ГАЗ-21, ГАЗ-24 и их менее
легендарные потомки. Только цех этот выскребли до штукатурки,
вооружили до зубов современным оборудованием и делают «Йети», к которому
буквально сейчас присоединилась Jetta,
а летом – новая Octavia.
Так что это – совместное предприятие или просто долгосрочная аренда помещений?
Это контрактная сборка – был ответ. В этот минизавод внутри
промышленного гиганта Volkswagen
и группа «ГАЗ» вложились совместно (хотя львиная доля акций, естественно, у Volkswagen), а роли
распределили так. Оборудование, технологии, обучение – это «фольксвагеновское».
Но за само производство отвечает группа «ГАЗ»: рабочие в основном российские,
руководители – тоже. Есть чехи и немцы, но это на первое время, чтобы задать
планку и помочь с обучением.
И тут уже закрадываются смутные мысли, а не получится ли как
всегда… Нет – контроль качества или, как его здесь называют, аудит –
прерогатива европейской стороны. Собственно, во время сборки автомобиль еще не
является ни «Шкодой», ни «Фольксвагеном». Этот почетный статус он получает
после прохождения поста финального контроля качества, где работают
представители Volkswagen,
причем, в постоянной ротации – чтобы исключить элемент кумовства. Это
посторонние для заводчан люди, в некотором смысле обезличенные – результаты
своих проверок они «публикуют» в виде листка А4. Если обнаруженный недостаток
можно устранить в заводской мастерской – это делают и автомобиль проверяют
по-новой. Если же нет – машину пускают «на органы», часть компонентов просто
утилизируют. Только пройдя все тесты
автомобиль получает «паспорт Фольксвагена». 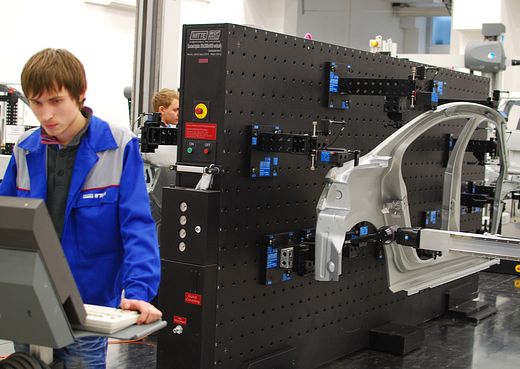
Аудиторы наведываются и на само производство, проверяя все и
вся. Они могут ткнуть пальцем в кузов и отправить его на измерительный стенд,
щуп которого сделан из рубина. Они изучают статистические данные о контроле
тысяч параметров, которые фиксируются на каждом этапе производства автомобиля.
Сама система контроля качества построена по принципу петель:
любой брак стараются обнаружить как можно раньше и сделать операцию по-новой,
если возможно. Допустим, сварщик обязан проверить свариваемые компоненты на «адекватность»,
если что-то не устраивает – деталь откладывают в сторону для дальнейших
разбирательств. Сварщик отвечает за непровары. Двигаясь по технологической
цепочке 3-минутными тактами, автомобиль постоянно подвергается тестам, органолептическим
или инструментальным. «Потому что чем позже мы обнаружим ошибку, тем дороже она
нам обойдется», - говорит Моймир.
А вот кузова проверили в дождевальной камере. На стенд
вывешивается листок следующего содержания:
«Водный тест. Количество проверенных автомобилей – 22. Вода
в заднем кармане (1). Неверное нанесение пластизоля. Отв. – окраска».
Собственно, наличие осечек само по себе некртично – они бывают
всегда. Разница лишь в том, выявил ли производитель проблему или закрыл глаза.
Моймир говорит, что скоро на линии смонтируют дорогущий
стенд Leika, который в «прямом
эфире» будет проводить оптическое измерение геометрии 100% кузов. Сейчас примерно
два кузова в смену снимается с конвейера и промеряется теми самыми «рубиновыми щупами»
по всем ключевым точкам. 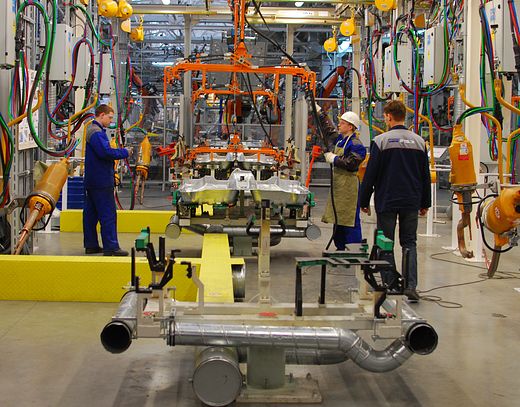
Полная техническая документация на автомобиль, включая
фамилии рабочих, имевших отношение к данному автомобилю, хранится 15 лет, так
что если вдруг проблема всплывет даже после продажи автомобиля, Volkswagen сможет понять
причину ее появления.
Изнутри завод выглядит точь-в-точь, как предприятия в
Квасинах, Млада-Болеславе и Калуге – наличие автомобильной истории у этого
места не имело значение. От прежнего производства «ГАЗа» остались несколько
роботов Kuka, которые
покупались для «Сайбера» - собственно, роботы почти на всех автозаводах
одинаковые. В остальном дух «Волги» отсюда вытравили до такой степени, что
выходя из цеха впадаешь в ступор – на улице что-то вроде ЧТЗ. Старые рельсы,
старые погрузчики, «Спасибо за добросовестный труд» над проходной. Это два
разных мира, словно кусок Европы телепортировали в самое сердце российского
автопрома.
Volkswagen
вложил в завод 200 миллионов долларов и имеет большие планы. Сейчас выпускается
одна модель в одну смену. Через полгода здесь будут делать три модели в три
смены. В этом году выпустят 56 тысяч машин (22 тысячи «Джетт», 13 тысяч «Йети»,
21 тысячу «Октавий»), проектная мощность при пятидневной неделе – 110 тысяч, а
если захватить и субботу – 130 тысяч.
Когда ходишь по территории от цеха к цеху, то и дело
уворачиваешься от Chevrolet Aveo:
их собирают тут же, на «ГАЗе», естественно, в отдельных от Volkswagen цехах. Но у «Шевроле» проект
поскромнее – контракт на 4 года, инвестиции – 30 миллионов долларов. «И машины
у них приходят в одной коробке в разобранном виде – наверное, для упрощения
сборки. У нас налажена обычная для Европы схема логистики, когда детали едут со
всего мира «порознь», - объясняют шкодовцы (я не придумал мнемонических правил
для всех, но мы встретили пять или шесть чехов-руководителей).
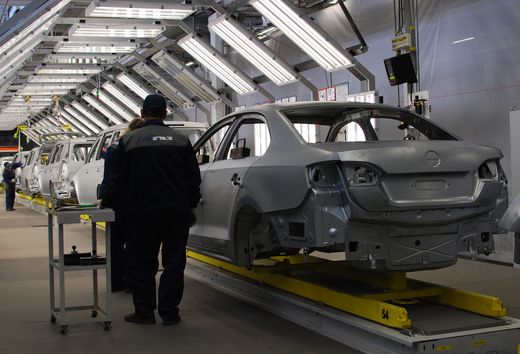
Резоны Volkswagen понятны: они
получили готовый цех и всю инфраструктуру. Резоны «ГАЗа» также очевидны: после
провала «Сайбера» и окончании производства «Волги», нужно было чем-то занять
цеха и людей. Полагаю, прагматичный Бо Андерсен, руководитель Группы «ГАЗ», не
колебался долго, потому что других альтернатив занять такие площади надолго
просто нет. Инженерный штаб самого «ГАЗа» работает над коммерческим
транспортом, который, в отличие от легковых «Волг», экономически выгоден и
имеет перспективу.
Кстати, соотношение рабочих, которые еще помнят «Волги», и
новобранцев – примерно 50:50. У Volkswagen нет предубеждения к бывшим работникам
предприятия, потому что человек, включенный в правильную систему, будет
работать правильно. Просто потому, что у него иного выбора. Вопреки привычному
в России мнению, не руки рабочих определяют качество продукта, а голова
руководителя.
Однако любой рабочий Volkswagen должен пройти полное обучение в специальном учебном
центре и неважно, сколько миллионов затянутых гаек было в его карьере.
Руководитель учебного центра Иван говорит: «Приходят
рабочие, которые стояли на конвейере с гайковертом и говорят – ну что вы,
будете учить нас, как гайковерт держать? И мы показываем им, какой должна быть
поза и положение рук, чтобы не развились болезни суставов. И они удивляются –
20 лет работал, мучился, и не знал».
Можно прийти с улицы – никаких особых требований к кандидату
нет. Обучение длится всего неделю, затем – две недели стажировки в цеху, и если
все хорошо – вперед. Я удивляюсь: что, за три недели можно стать рабочим? А в
ПТУ вон годами учат…
«Да брось, - говорит Иван. – Когда я пришел на конвейер «ГАЗа»,
меня не учили ни дня. Я просто вышел утром на работу и стал сварщиком».
В учебном центре обучение весьма забавное: есть, конечно,
теория, но много заданий, напоминающих игру. Например, на учебной доске
приколоты этак сотня карточек с цифрами, да все еще разными шрифтами – что-то
вроде «капчи». Человеку нужно быстро отыскать среди них цифры от 1 до 60, допустим,
и перечеркнуть каждую фломастером. Умные выстраивают их в рядок и черкают
оптом.
Есть, конечно, и более конкретные тренировки, например,
сварщики упражняются с настоящими клещами, водители автопогрузчиков учатся
грузить огромные лари на верхние этажи стеллажей, а маляры красят водой.
Некоторые задание с подвохом: например, сборщикам на
конвейере дают заведомо «кривую» технологическую карту, проверяя, смогут ли они
найти ошибку. Да, из человека здесь делают биоробота, но ведь и робот должен
быть адекватным. 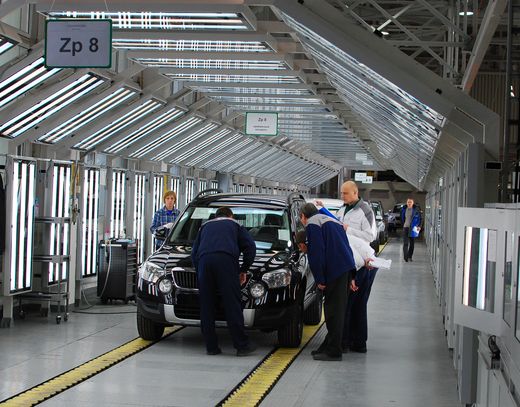
Напоследок я поговорил с нижегородцами. Как им все эти
перемены? К Бо Андерсону и Группе «ГАЗ» здесь относятся с уважением: завод был
на грани краха, а теперь развивается. Присутствие «интервентов», конечно,
кого-то смущает, но если смотреть на вещи реально, другого пути и не было.
Российский автопром, как феномен, умер. Почти.
|